Which industrial sealant is right for your application
June 11th at 11:26am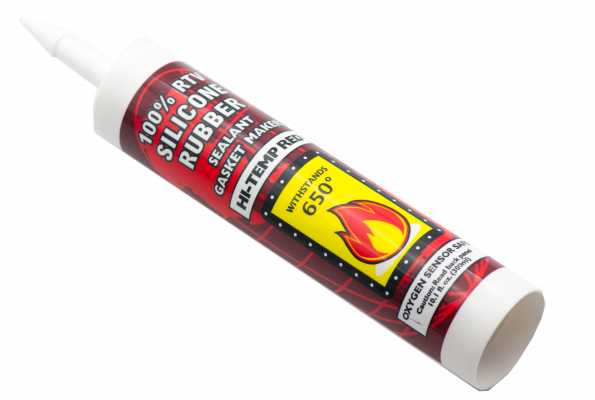
What is a sealant?
Sealant is a type of mechanical seal that is widely used in domestic and industrial applications in order to fill up unwanted gaps and openings that may cause the seepage of water, gases or any particulate matter. Mating of two or more parts together results in gaps, which adversely affect the integrity and the performance of the object. Sealants are effectively used to fill up gaps between the surfaces and close off any spaces that may occur. However, sealants are not an alternative to adhesives while some sealants do have adhesive properties.
Curing is a process under which the applied sealant is toughed or allowed to settle down effectively. The curing process and duration is solely based on which sealant is being applied to the joints. Curing process for some sealants may take few hours whereas for some it may take up to weeks. The methods that are used to cure different types of sealants are as follows;What is curing?
- Ambient temperature
Under this curing procedure, the sealant is applied at the joint and left untouched at room temperature. The moisture in the air cures the sealant. Ambient temperature sealant usually have a curing time from thirty minutes to four hours. The thickness layer of the sealant as well as the ambient humidity directly affects curing time. Silicone and epoxy sealants are usually cured using this method.
Thermal curing
- For the thermally cured sealants, the sealants do not reach its full toughness and hardness until it has been heated to a specific temperature. The sealants that are thermally cured fall under two distinct categories namely - Thermoplastic sealant, and Thermosetting sealants. Polymer sealants are usually cured using this method of curing.
- Anaerobic curing
Anaerobic curing is the curing of the sealants that cure in the absence of oxygen. Anaerobic sealants are usually used in the metal joining while exposing them to metal ions.
- UV light/Radiation
Ultraviolent light or electron beams are used to cure the sealant instead of applying heat using some external heat source. This method of curing is advantageous as it demands less energy consumption and quicker cure times. Acrylic sealants can be cured using this method of curing.
Types of sealants
Currently, there are more than forty types of sealants available in the market, out of which the most commonly industrially used sealants are as follows:
- Silicone
Silicone sealants are one of the most commonly used sealants. Silicone sealants exists in either neutral cure or acetoxy. The production of silicone sealants involves an extensive polymerization and hydrolysis process of siloxanes and silanes. Both the neutral and acetoxy silicone sealants cures at the room temperature and are compatible with a variety of materials. Acetoxy silicone sealants are cheaper than its counterpart and offers quicker cure time. Acetoxy silicones are however, incompatible to perform a seal between subtracts that might react with acids. Neutral cure silicon sealants have a slower cure time and a bit more expensive to produce as compared to acetoxy. Silicone sealants have a life expectancy to around 10-20 years after application.
- Epoxy
Epoxy sealants are usually supplied in a two-pack configurations consisting of a resin and a hardener. They are mixed together in pre-set ratio for the epoxy to perform its joint sealing. Epoxy sealants are well known for their high strengths, exceptional cure toughness and the ability to resist the environmental or chemical damage to the sealing. Epoxy sealants are one of the few sealants that also holds great strength to act as an adhesive. Epoxy sealants cure at room temperature whereas; in some case they might be required to be cured thermally.
- Phenolic Sealant
Phenolic sealants are types of resins that provides effective bonding and have a good endurance rating against high temperature. Phenolic sealants is the only sealant that is available in powder, liquid and film form. The phenolic sealant is usually composed of phenol and formaldehyde chemicals.
- Acrylic sealant
Acrylic sealants are processed from acrylic acid (hence acrylic sealant) via catalytic reaction. Acrylic sealants are highly resistant to degradation caused by environment. Acrylic sealants however, are prone to chemical damage. Acrylic sealant is curable via many different ways however, if thermally cured; the curing time is lowered significantly. Acrylic sealants have a high holding power and avoids any infiltration by foreign particles.
- Polymers
The group of polymers that makes up this category of sealant includes polyesters, polyamide, polysulfide and vinyl. The polymers forms a permanent flexible seal at the joint and uses the moisture in the air to cure. Polymer sealants are ideal to be applied on joints that encounters repetitive movements or are subjected to a varying temperature. One of the drawback to polymer sealant is that it requires the most curing time as compared to the rest of the sealants. Therefore, polymer sealants once applied to a joint are kept untouched for a long duration of time.
Industrial applications
- Silicone
Due to its ease of use, durability and being room temperature vulcanisable (RTV), silicone is the most commonly used sealant both domestically and industrially. Silicone is widely used in the sealing of high-rise building, bridge joints and various weatherproofing purposes. Silicone being water-resistant is also used extensively in the sealing of sanitary joints in houses. Silicone is also the primary sealant used for the sealing of electric sockets, wires and fire-rated joints. Silicone having a high strength after being cured properly are also used in the structural glazing where they act as a load-bearing structure. The famous Burj-Al-Arab is a marvel of engineering sporting the silicone structural glazing.
- Epoxy: Epoxy is extensively used in industries due to its good sealing and adhesive nature. Epoxy is used in paint industries as it provides an excellent protective layer. Epoxy sealants are also used in automotive, aviation and boat industries as they provide good structural integrity. Electronic industries makes a vast use of epoxy sealants due to their non-conductive and quick drying nature. Hybrid circuits, PCB’s and integrated circuits all make use of epoxy to seal up the joint gaps. Floor joints of heavy traffic usage and swimming pools are also sealed using epoxy sealants.
- Phenolic Sealant: Phenolic sealants are used in the adhesive and sealing purposes of plywood, constructing buildings and appliance industry.
- Acrylic sealant: The acrylic sealants are most commonly used in sealing doors and window frames. Acrylic sealants are used for caulking, jointing and grouting purposes. Acrylic sealants being odorless and easily paintable are most commonly used in sealing household joints. Acrylic sealants however, are not advised to be used on glass panes due to their flexibility.
- Polymers: Polymer sealants are most commonly consumed at locations requiring expansion joints. Brickwork and bridge joints usually have polymer sealing between them. Polymer glazing is also used in capping glazing purposes.
Material compatibility
To decide which sealant to use of all the available sealants, it must be made sure before application that whether the joining material is compatible or not. Having a sealant being applied on an incompatible material may result in the degradation of the material and failure to seal off the joint.
- Porous surfaces: Porous surfaces have the best compatibility with sealants having a high viscosity or gel like texture. Silicone, polymers and epoxies are the best-suited sealants for porous materials.
- Concrete: Concrete is the constructing material that is used for construction of buildings, walls and other structures. Polymer sealants are usually used to seal concrete joints.
- Metal: Metal joints are usually sealed together using silicone and polymer based sealants. Silicone is highly compatible with iron, aluminum, steel and iron compounds.
- Ceramics: Ceramics are the oxides and nitrides that are non-metal and have a high melting and boiling point. Ceramics can be sealed off using epoxy, silicone and acrylic sealants.
- Textiles: Textiles are most compatible with silicone-based sealants.
- Plastics: Plastics are the organic, process or synthetic materials obtained from polymer. Silicone and polymer acts as the most suitable sealants.
Sealant type | Cure procedure | Material Compatibility | ||||||
Concrete | Plastic | Ceramic | Textile | Porous | Metal | Rubber | ||
Silicone | Room temperature |
| X | X | X | X | X | X |
Epoxy | Room temperature |
|
| X |
| X |
| X |
Phenolic Sealant | Various |
|
|
| X |
|
|
|
Acrylic sealant | Various |
|
| X |
|
|
|
|
Polymers | Thermoplastic | X | X |
|
| X | X | X |
An easy guide to apply a sealant
The following pictures provides an easy step-by-step guide to perform a well-sealed joint.
Step one – Clean up the surface: Clean the surface with a cloth and make sure that the joints are dry and grease and dirt free.
Step two – Prepare the joints: Prepare the joints by aligning them in the way you want them to be sealed. Put masking tape around the edges in order to avoid any mess.
Step three – Apply masking tape: Insert backing material between the joints. Addition of a backing material avoids the seepage of sealant deep into the joint during curing process.
Step four – Application of sealant: The sealant is applied manually or using a sealant applying machine. Handguns are the most common type of sealant applicators.
Step five – Joint smoothing: The joint is smoothed out using a plastic card. This allows for a better sealant contact with the joint.
Step six – Remove the masking tape: After all the previous steps are completed accordingly, the masking tapes are removed. Allow some time to cure if the sealant is cured at ambient temperature.
Other Posts
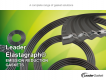
ElastaGraph - A Revolutionary Metal Gasket Technology
Read Article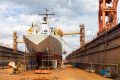
How do IMPA Marine Numbers Map to Phelps Industrial's Products
Read ArticleHow to chose O-Ring material for your fluid sealing applications
Read Article
Troubleshooting O-Ring Failures
Read Article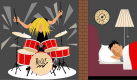