How to chose O-Ring material for your fluid sealing applications
October 8th at 7:43pmO-ring are one of the most commonly used fluid power seals. These seals have a simple donut-shaped ring (technically called a toroid) and are manufactured using pliable material such as elastomers like silicone, Buna-N and Ethylene-Propylene. O-rings are installed in order to seal off connections between connectors, pipes, tubes, etc. via mechanical deformation. Once installed, O-rings make sure that no liquid or air sweep through the designated area.
Since O-rings are crucial to perform effectively after being installed, selecting the right O-ring material is crucial. The crash of space shuttle Challenger in 1986 is a well-documented case of what failure of O-rings can do. Today O-rings are manufactured using thousands of different materials and every material perform differently under several conditions. The following sections includes the most commonly materials used for the O-rings, their working temperature, the shore A hardness scores, the standard colors as well as the limitations of that materials. Complete O-ring material compatibility for various applications can be found here.
Seal material: Alfas® Hardness (Shore A): 60 -90 Standard Colour: Black Working temperature: -14° to +446°F (Standard Compound) Key uses: Used in seals for aerospace, oil related seals. Commonly used in industrial environment. Features: Can be used in variety of seals due to high temperature and chemical resistance. Limitations: Not recommended to be used in seals concerning toluene, ether, ketone and acetic acid | ![]() |
Seal material: Fluorocarbons Hardness (Shore A): 55 to 90 Standard Colour: Black Working temperature:-13°to+446°F (Standard Compound) 40°to+446°F (Special Compound) Key uses: Fluorocarbons are widely used in sealing off aircraft’s engines. They are also used sealing of automotive fuels handling systems. Fluorocarbons can be used to in seals having low compression or high temperature Features: High fluorine grade O-rings gives better performance in methanol/ethanol blended gasoline. Base resistant grade offers better oil protection. They can also endure high temperature. Special compounds, using new polymer technologies, provide improved low temperature performance with a TR (10) of -40°F and brittleness to -76°F. Limitations: O-rings of fluorocarbons should not be exposed to amines, low molecular weight esters and ethers, amines, nitro hydrocarbons, Skydrol® fluids or hot hydrofluoric acids. Fluorocarbons are not recommended on dynamic seals at low temperature | ![]() |
Seal material: Buna-N Hardness (Shore A): 40-90 Standard Colour: Black Working temperature: -40° to +257°F (Standard Compound) Key uses: Is resistance to all types of oil. Can be used for aerospace purposes and off-road equipment .Buna-n can be compounded for FDA applications. Features: Can be compounded to work as low as -85°F. Can be formulated to be more abrasion resistant. Limitations: Prone to ozone reaction. Buna-N O-rings usually have phthalate type plasticizers. They may seep out and cause issues for certain plastics. | ![]() |
Seal material: Butyl Hardness (Shore A): 30 to 90 Standard Colour: Black Working temperature: 50° to +250°F. (Standard compound) Key uses: highly effective in hydraulic systems and vacuum sealing. Features: Have one of the lowest permeability to gases. Inert to ozone reactions and sunlight aging. Butyl also hold excellent shock absorbing abilities. Limitations: Being a petroleum product, butyl is reactive to hydrocarbon solvents and oils. | ![]() |
Seal material: Perfluoroelastomer Hardness (Shore A): 65 to 90 Standard Colour: Black Working temperature: -13°F to +600°F Standard Compound Key uses: Used in seals in chemical and petroleum industries. Perfluoroelastomer can be used for locations having high temperatures. Perfluoroelastomer can also be used for paint and coating operations. Features: FFKM combines the toughness of an elastomeric material with the chemical inertness of Teflon® . It resists attack by nearly all chemical reagents and provides long-term service where corrosive additives can cause other elastomers to swell or degrade. In addition, FFKM parts are less likely to cold flow than Teflon seals. Limitations: Withstanding degradation by virtually ALL chemicals, Perfluoroelastomer can swell significantly when exposed to some fluorinated solvents. Perfluoroelastomer parts should not be exposed to molten or gaseous alkali metals. Perfluoroelastomer are not cost effective and used only when no other elastomer is suitable to be used. | ![]() |
Seal material: Fluorosilicone Hardness (Shore A): 40 to 80 Standard Colour: Blue Working temperature: 75°F to +400°F Standard Compound Key uses: Fluorosilicone is primarily used for static sealing. Fluorosilicone is used in seals of air fuel emission control system and aerospace fuel system. Features: Fluorosilicone is most often used in aerospace applications for systems requiring fuel resistance up to 400°F. Fluorosilicone also features good compression set and resilience properties. Fluorosilicone compounds can be exposed to air, sunlight, ozone, chlorinated and aromatic hydrocarbons and still function effectively. Limitations: Not recommended for dynamic sealing due to limited physical strength, poor abrasion resistance, and high friction characteristics. Exposure to hydrazine, ketones and brake fluids is not recommended. | ![]() |
Seal material: Silicone Hardness (Shore A): 20-80 Standard Colour: Red Working temperature: -85° to 400° F Key uses: Widely used in high temperature seals. Features: Phenyl based silicones can work to extremes of -148°F Limitations: Low abrasion and tear resistance. Not effective at dynamic seals. Highly permeable to gases. Avoid use at seals with concentrated acid. | ![]() |
Seal material: Natural Rubber Hardness (Shore A): 40-90 Standard Colour: Black, Brown/Beige Working temperature: -58°F to +158°F Standard Compound: Key uses: One of the most widely used material in seals of everyday applications. Used in seals of food and beverages. Natural rubber seals are widely used to for non-hydraulic sealing applications. Natural rubber seals also have the ability to absorb vibrations therefore, are used for dampeners as well. Features: Has high tensile strength, high resilience, high abrasion and high tear resistance. Natural rubber has good adhering to metals. Natural rubber also provides excellent resistance to organic compounds such as alcohols and acids. Before the invent of synthetic elastomers in 1930’s, O-rings were only manufactured using natural rubber. Limitations: Poor compression set performance. Lack resistance to many fluid flows. Not recommended to be used for industrial purposes. | ![]() |
Seal material: Polyacrylate Hardness (Shore A): 40 to 90 Standard Colour: Black Working temperature: -25°F to +300°F, Standard Compound Key uses: Widely used in Sealing of automatic transmissions & automotive power steering systems. Polyacrylate is also used for sealing petroleum oils up to 300°F. Features: Highly resistant to sunlight and ozone degradation, Polyacrylate also features an enhanced ability to resist flex cracking. Limitations: Polyacrylate do not perform well under at low temperatures and has bad water resistance. Polyacrylate also has inferior performance on compression set. | ![]() |
Seal material: Teflon® (Polytetrafluoroethylene) Hardness (Shore A): 98 Standard Colour: White Working temperature: -300 °F to +450°F (Standard compound) Key uses: Widely used in static and slow intermittent dynamic seals. Features: Virtually inert to almost all the industry chemicals. Teflon also performs well with different chemicals at high temperatures as well. Teflon has high endurance ratings. Teflon have high resistance to ozone and degradation effects due to exposure to acetones, xylene and MEK. Teflon are tough and have low friction. Limitations: One of the biggest limitations is the poor elastic memory at both low and room temperature. This poses a problem while installation of Teflon seals. They need to be heated pre-installation to ensure a tight fit. This causes the overall installation of Teflon seals to be a bit more expensive as compared to the rest of the seals. Teflon also has a poor tear resistance therefore, cannot be installed on dynamic seals. | ![]() |
Seal material: Polyurethane, Cast Hardness (Shore A): 70-90 Standard Colour: Amber Working temperature: -30°F to +175°F (Standard Compound) Key uses: Ideal for high hydraulic pressure seals. They are highly effective at seals subjected to high stress. Their shock absorbing nature is utilized by using them in wheels, bumper coupler and rolls. Good for dynamic seals Features: Have a high tensile strength of up to 6000 psi. Elongations up to 300 to 650% of the original size. This allows them to be used effectively ion the dynamic seals. Polyurethane also have an exceptionally high abrasion resistance. Compatible with weak acids and bases as well as hydraulic fluids. Polyurethane seals can be used with mixture containing less than 80% aromatic constituents. Limitations: One of the drawbacks of cast polyurethanes is their ineffectiveness when exposed to esters, ketones and concentrated bases and acids. Cast Polyurethane are also not recommended to be used on their own with steam or hot water. | ![]() |
Seal material: Polyurethane, Millable Hardness (Shore A): 40-90 Standard Colour: Black Working temperature: -30°F to +175°F (Standard condition) Key uses: Highly effective for static seals. Millable Polyurethane can also withstand high temperature. Millable Polyurethane seals are widely used in medical devices and is compatible with FDA regulations. Features: Millable Polyurethane have a good performance with seals installed at hydraulic situations. Millable Polyurethane have a superior performance at locations having high pressure and shock loads. Millable Polyurethane are also prone to any damage by petroleum-based oils, hydraulic fluids or hydrocarbons. Millable Polyurethane also have a good tear resistance and do age rapidly under sunlight. Limitations: Millable Polyurethane loses its strength and at time shapes at high temperatures. Not recommended at locations subjected to high temperature. Millable Polyurethane also have a tendency to be spoilt if exposed to concentrated acids, ketones and acids. Likely to deteriorate when exposed to steam or hot water. | ![]() |
Please call our sealing experts @ 1-800-876-SEAL
Other Posts
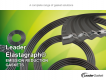
ElastaGraph - A Revolutionary Metal Gasket Technology
Read Article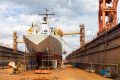
How do IMPA Marine Numbers Map to Phelps Industrial's Products
Read Article
Troubleshooting O-Ring Failures
Read Article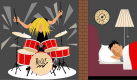
Material for Sound Proofing and Sound Dampening
Read Article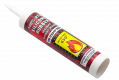